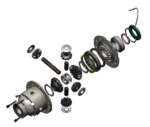
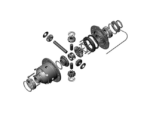
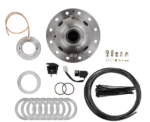
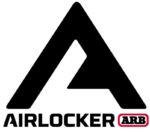
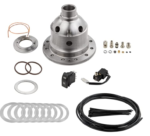
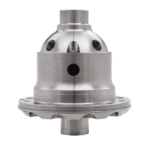
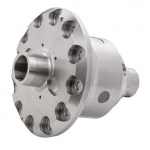
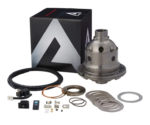
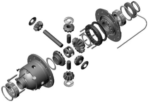
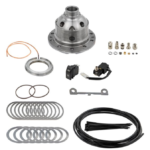
Ford E-Series E150 | E250 | E350 | E450 ARB Driveline/Transmission Differential Air Locker
$1,295.95 Original price was: $1,295.95.$1,175.00Current price is: $1,175.00.
Tax Included Pricing
ARB Airlocker 35 Spl Sterling/Corp Ford 10.25&10.5In S/N (RD140) for Ford E-Series E150 | E250 | E350 | E450
Contact us with your VIN we will find the right part for you!
FEATURES
- Provides 100% traction on demand without affecting on road drivability or driveline wear
- Vastly improved traction means less reliance on momentum, which reduces the likelihood of vehicle damage and environmental impact
- Easy, convenient operation allows the user to concentrate on the terrain without leaving the comfort and safety of the driver’s seat
- Ultra durable and extremely strong – only the highest quality materials used in construction
- Incredibly simple yet effective design that employs minimal moving parts, thereby ensuring maximum reliability
- Thoroughly tested and proven design – trusted and used in over 80 countries around the world
- Front and rear Air Lockers available for most makes and models
- 4WD & 2WD applications
- Easy installation and maintenance – no special tools, skills or additives required
- Leading Manufacturer Of High-Quality Products
- International Renown For Our Diverse Range Of Award-Winning Products
- Designed With The User In Mind
- Proven And Tested For Durability And Function In Real-World Conditions
- Meeting Or Exceeding All Required And Standardized Testing
AIR LOCKER DESIGN AND ENGINEERING
A relentless commitment to research and design, the use of high quality materials and an uncompromising approach to manufacturing have all contributed to Air Locker’s success in over 100 countries worldwide. The patented design of the ARB Air Locker is extremely strong, with structural components manufactured from aerospace grades of alloy steel.
Recent developments have seen forged gears and an improved two piece design add increased strength and durability, while reducing the amount of moving parts to ensure precision amongst components and a much firmer and responsive activation. These additions have also resulted in increased load bearing capabilities.
The design process of an Air Locker involves countless hours of testing. Computerised Finite Element Analysis (FEA) allows the engineer to subject each Air Locker design to ‘virtual’ off road driving stress simulations much more extreme than those experienced in real life, including extreme temperatures and harsh wheel-spin. Prototypes are tested to ensure the strength of the Air Locker exceeds that of the axles or other driveline components. Finally, field testing is carried out with units being fitted to 4x4s that operated in the harshest environments imaginable.
Once this exhaustive design phase is complete, ARB Air Lockers are manufactured in Australia by ARB and sold throughout the world.
For peace of mind, all ARB Air Lockers are backed by an industry leading five year warranty.
AIR LOCKERS IN COMPETITION
Of the many ARB products seen in off road competition, it’s the one you can’t see that makes the difference – ARB Air Locker diff locks continue to dominate the world’s toughest off road events.
ARB Air Lockers are used in extreme off road competitions the world over. ARB’s commitment to research, development, design and production means ARB Air Lockers set the benchmark for quality and reliability – two things crucial to competition use. So if you need traction you can rely on, rely on ARB Air Lockers….the world’s best already do.
AIR LOCKER WINNER OF
- King of the Hammers
- Ultra4 Series
- Baja 1000/500
- Mexico 500
- W.E.Rock Dirt Riot
- W.E.Rock Rock Crawl
- Outback Challenge
- USA Extreme Rock Crawling Series
- Tuff Truck Challenge
PERFORMANCE MODEL LINE
ARB Air Lockers are available for the vast majority of 4×4 vehicles from around the world. In addition, a number of high performance models are available for specialist applications such as drag racing, competition rock crawling and heavy tank-track type snow equipment.
Designing locking differentials for applications such as these presented our engineering team with some significant challenges. Not only must the locker be able to withstand more traction torque than a standard differential, but it must also tolerate massive amounts of torque handling facilitated by the substitution of custom made high alloy aftermarket axle shafts, which are cut with larger than standard diameter splines. This is particularly difficult owing to size constraints dictated by the original axle assembly. ARB met this challenge using a combination of aerospace grade materials, and a design guided by the results of high torque testing using computer simulations and destructive testing.
Weight | 11 lbs |
---|---|
Dimensions | 11 × 11 × 11 in |